Printing Maine’s Future
How a research and development team at the University of Maine printed the largest 3-D object in the world
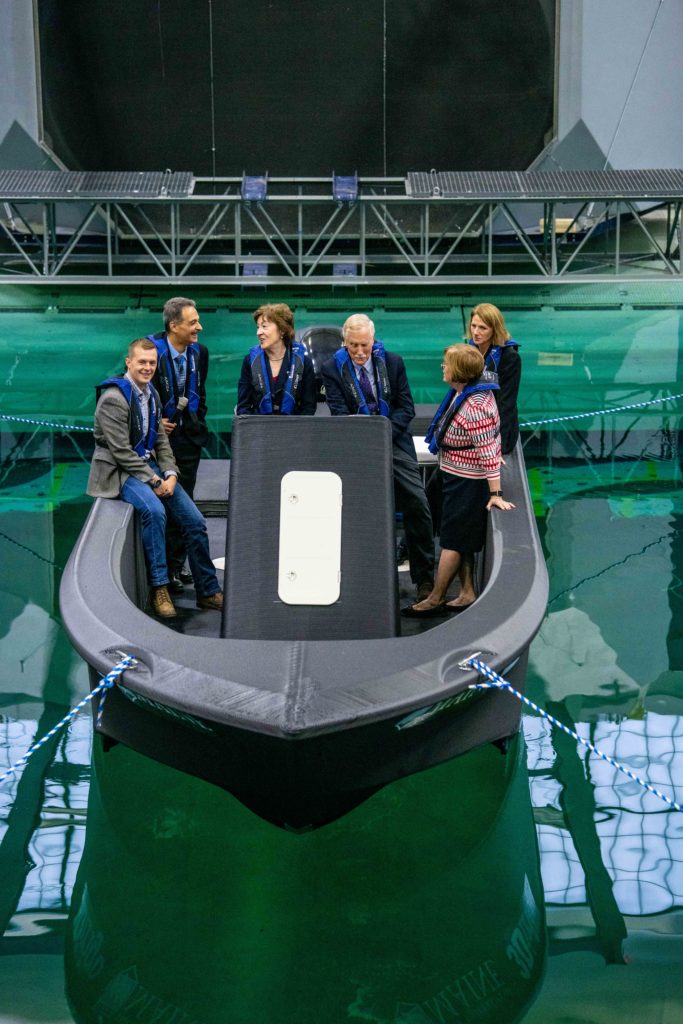
It started as a glob of bioplastic. At the end of 72 hours, it was a 25-foot-long patrol boat weighing 5,000 pounds. The University of Maine’s Advanced Structures and Composites Center made national headlines last October when it unveiled the vessel—the largest 3-D printed object in the world, printed by the largest 3-D printer—but that result seemed far from certain just weeks before the public unveiling.
The team had the printer up and running in the middle of September, but they didn’t know if it would be possible to print a boat, says Habib Dagher, executive director of the Advanced Structures and Composites Center. No one had printed anything that large before, and furthermore, a boat is a unique challenge because of its hollow form. There was also a deadline: the center planned to showcase the printer at an October 10 public announcement of the project. The company that made the printer, Ingersoll Machine Tools in Rockford, Illinois, doubted the team could print a boat by then. “They said it wasn’t possible,” says James Anderson, the senior research and development program manager at the center who helped oversee the project. “They didn’t really want to support the process, because they didn’t want it to fail.” Dagher had to call the manufacturing company’s CEO to convince him to approve the project.
To overcome the challenge of printing a hollow object, the team developed a patent-pending method to print at a 45-degree angle. Anderson, who previously worked as director of engineering at Hodgdon Yachts, used his own 3-D printer to make small-scale versions of the hull design to troubleshoot any printing issues. The printing process began the night of September 19 and finished September 22 at 10:15 p.m. Once it was finished, everyone climbed up on the boat and looked around. “There was just elation and exuberance,” Anderson says.
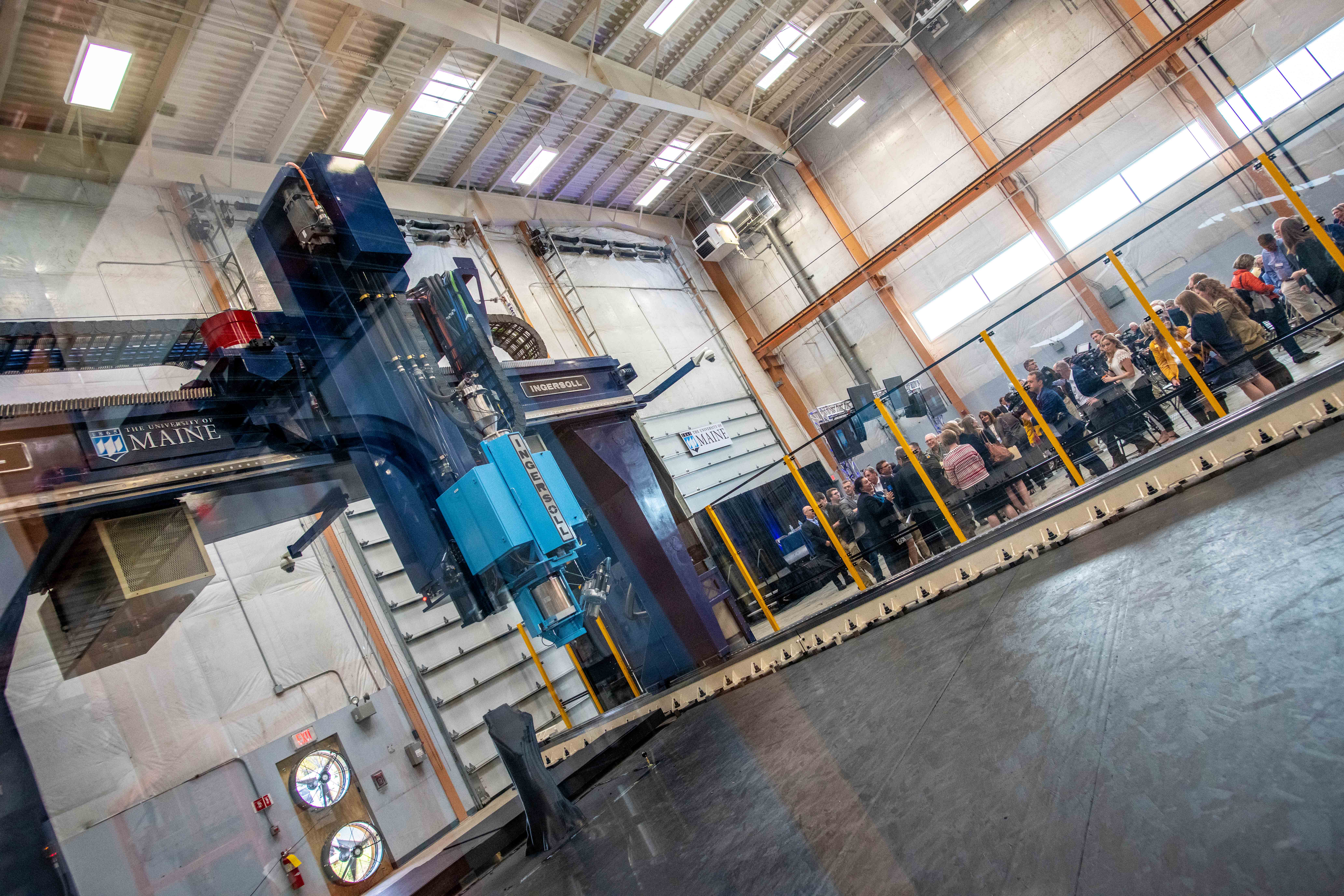
But even after the boat was complete, uncertainty remained: “We didn’t know if it was going to float,” says Dagher. “We hadn’t done this before. We were truly going into the complete unknown.” In the end, Maine’s congressional delegation joined Dagher on the boat in the center’s wave tank during the public unveiling.
The next goal of the project, which is a $20 million research collaboration with the U.S. Department of Energy’s Oak Ridge National Laboratory, is to increase the amount of cellulose fibers in the bioplastic to 50 percent to make boat molds that are recyclable and more economical. The center has also received inquiries from around the world about using the printer to make other objects, from buildings to magnetic levitation train cars, says Dagher. “It’s going to open up and allow entrepreneurs in Maine and beyond Maine to realize things they’ve never realized before.”